The Ultimate Guide to Marine Rubber Fender-Types, Applications, and Benefits
PRODUCT UPDATES
Jettyguard
5/28/202311 min read
Introduction
Marine rubber fenders are critical components of vessel and structure protection in ports, harbors, quays and offshore structures. They are designed to absorb impact energy from vessel berthing and protect both the vessel and the structure.
In this guide, we will explore the different types of marine rubber fenders, their applications, and their benefits.
1. What are Marine Rubber Fenders
1) Definition and History Marine rubber fenders are devices made of high-quality rubber material designed to provide protection to ships and other marine structures from damages caused by collisions. These devices have been in use since the 1950s when rubber was first used in the marine industry. Marine rubber fenders have since become essential components in the shipping industry, providing efficient protection to marine vessels and structures.
2) Composition and Construction Marine rubber fenders are made of high-quality rubber compounds reinforced with synthetic cords for additional strength. The rubber material used is resistant to corrosion and ultraviolet (UV) radiation, making it suitable for use in marine environments. These devices can be constructed in different shapes and sizes, depending on the intended use.
3) Common Sizes and Shapes Marine rubber fenders come in various shapes and sizes to cater to different marine structures and vessels. Some of the most common shapes include cylindrical, conical, cell, and arch fenders.
2. Importance of Marine Rubber Fenders for Vessel Protection
1) Risks of Berthing and Mooring Operations Vessels are exposed to different risks when berthing and mooring. These risks include impact forces from waves and tides, which can cause severe damage to both the vessel and the port structure. Berthing accidents can lead to significant financial losses, injuries, and even fatalities.
2) Benefits of Using Marine Rubber Fenders Marine rubber fenders provide a buffer between the vessel and the port structure, reducing the impact of collisions. This protection reduces the risks of vessel damage, which can lead to expensive repairs, downtime, and loss of revenue. Using marine rubber fenders also ensures the safety of the crew and reduces the risk of accidents and injuries.
Types of Marine Rubber Fenders
There are several types of marine rubber fenders, each with its unique design and function. The most common types of marine rubber fenders include
1. Arch Fenders
1) Description and Characteristics
Arch fenders are commonly used for small to medium-sized vessels. They have a curved design that provides a larger contact area and distributes the impact energy more evenly. Arch fenders can be installed horizontally or vertically, depending on the application.
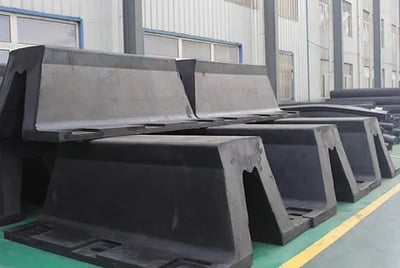
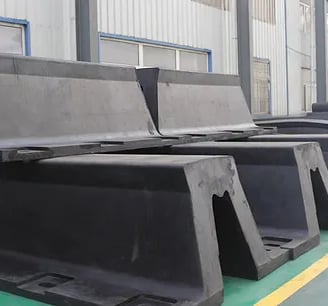
2) Applications
Arch fenders are commonly used in ports and harbors, where there is a need for protection against small to medium-sized vessels.
3) Advantages and Disadvantages
Arch fenders are relatively cheap, easy to install and maintain. However, they are not suitable for use in areas with high tidal ranges.
2. Cell Fenders
1) Description and Characteristics
Cell fenders are commonly used for large vessels, such as tankers and container ships. They have a hollow design that allows for compression and elongation during impact, which helps to absorb the impact energy. Cell fenders are often used in ports and harbors where there is a high tidal range.

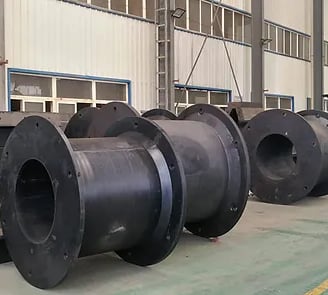
2) Applications
Cell fenders are commonly used in ports and harbors where there is a need for protection against large vessels, such as tankers and container ships.
3) Advantages and Disadvantages
Cell fenders have a high energy absorption capacity and can be used in areas with high tidal ranges. However, they are relatively expensive compared to other types of marine rubber fenders.
3. Cone Fenders
1) Description and Characteristics
Cone fenders are also a popular type of marine rubber fender, known for their high energy absorption capacity and low reaction force. They consist of a conical rubber body and a steel frontal frame and are designed to deflect the vessel's energy through the fender's surface area, providing a large contact area for the vessel to berth. They are suitable for a variety of berthing conditions and are commonly used in terminals with large vessels and high tidal variations. Cone fenders are available in different sizes and can be customized to suit specific requirements

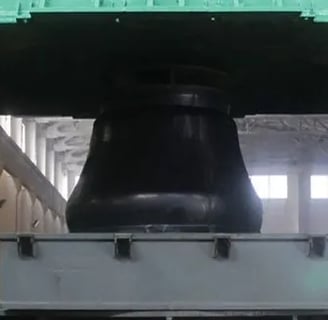
2) Applications
Cone fenders are suitable for a wide range of applications, including large tanker and container vessels, bulk carriers, and cruise ships. They are also used in ship-to-ship operations and offshore facilities. Cone fenders are ideal for berths with high-energy conditions, where the vessel's berthing velocity is relatively high, or the tidal range is significant. They are commonly used in oil and gas terminals, container terminals, and general cargo terminals.
3) Advantages and Disadvantages
Cone fenders have several advantages, including their high energy absorption capacity, low reaction force, and large contact area. They are suitable for a wide range of berthing conditions and can be customized to meet specific requirements. However, they also have some disadvantages. Cone fenders require more space than other fender types and are relatively expensive compared to other options.
4. Cylindrical Fenders
1) Description and Characteristics
Cylindrical fenders are the oldest and most commonly used type of marine rubber fender. They consist of a hollow cylinder made of rubber and can be installed horizontally or vertically. Cylindrical fenders are available in various sizes and can be customized to meet specific requirements.
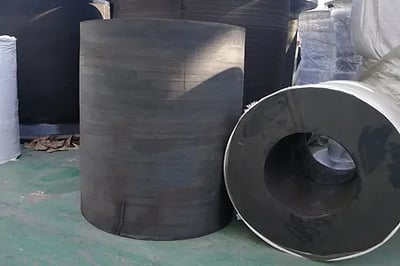
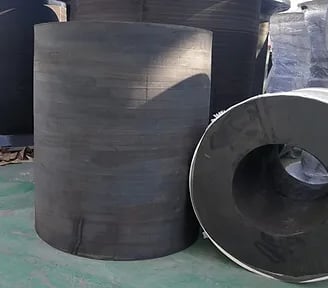
2) Applications
Cylindrical fenders are used in various applications, including ports and harbors, shipyards, and offshore facilities. They are suitable for small and medium-sized vessels and are commonly used for berthing and mooring operations. Cylindrical fenders are also used for ship-to-ship operations and as a protective barrier for offshore structures.
3) Advantages and Disadvantages
Cylindrical fenders have several advantages, including their versatility, durability, and cost-effectiveness. They are suitable for a wide range of applications and can be customized to meet specific requirements. However, they also have some disadvantages. Cylindrical fenders have a relatively low energy absorption capacity and may not be suitable for larger vessels or high-energy berthing conditions.
5. Element Fenders
1) Description and Characteristics
Element fenders, also known as modular fenders, are made up of separate rubber and steel components that can be assembled into various shapes and sizes. The rubber components are typically made of high-quality, durable materials that are resistant to wear, tear, and degradation from exposure to sunlight and saltwater. The steel components are designed to provide structural support and stability, and they are usually galvanized or coated with an anti-corrosion layer to protect against rust and deterioration.
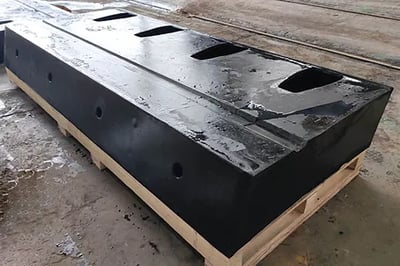
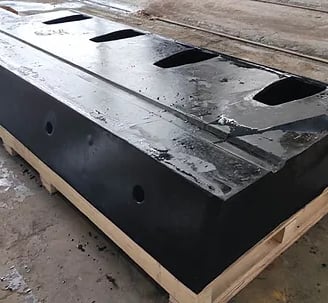
The modular design of element fenders makes them highly customizable and versatile, allowing them to be configured to meet the specific needs of different applications. They can be used to create straight, curved, or angled fenders, as well as combinations of these shapes. This flexibility in design makes them ideal for use in ports and harbors, where space constraints and varying vessel sizes and shapes require customized fender solutions.
2) Applications
Element fenders can be used in a wide range of marine applications, including
Protection of quay walls and berthing structures in ports and harbors
Protection of vessels during berthing and mooring operations
Protection of offshore structures, such as oil and gas platforms
Protection of navigational aids, such as buoys and beacons
3) Advantages and Disadvantages
Advantages
Highly customizable and versatile design
Can be configured to meet specific requirements of different applications
Durable and long-lasting
Easy to install and maintain
Can be easily replaced or repaired in case of damage.
Disadvantages
More expensive than some other types of fenders
Require more expertise to design and install than traditional fenders
May require more frequent maintenance and inspection due to their modular design
6. Pneumatic Fenders
1) Description and Characteristics
Pneumatic fenders, also known as air fenders or Yokohama fenders, are cylindrical fenders made of reinforced rubber with an air-filled inner chamber. They are typically constructed with several layers of rubber and nylon tire cord layers to provide strength and durability. Pneumatic fenders have a simple design and can be easily deflated and stored when not in use.
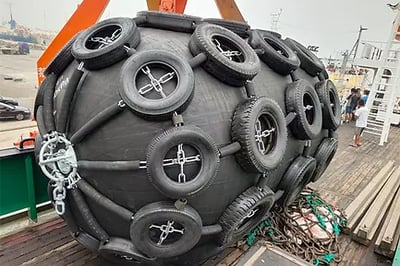
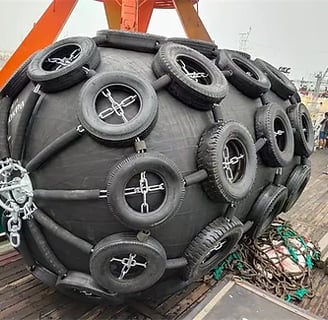
2) Applications
Pneumatic fenders are commonly used in various maritime applications, including ship-to-ship transfers, ship-to-dock operations, and as protective barriers for offshore structures. They are effective in absorbing impact energy and providing a cushioning effect during berthing and mooring operations. Pneumatic fenders are also suitable for use in areas with large tidal variations or in harsh marine environments.
3) Advantages and Disadvantages
Excellent energy absorption capabilities, making them suitable for high-energy berthing situations.
Easy to install, deflate, and relocate as needed.
Can withstand different berthing angles and vessel sizes.
Resistant to marine conditions, including UV exposure, seawater, and oil.
Disadvantages
Regular inspection and maintenance are required to ensure proper inflation and integrity.
Susceptible to punctures or damages from sharp objects or excessive impact.
Limited performance in extreme weather conditions, such as extremely low temperatures.
7. Foam-Filled Fenders:
1) Description and Characteristics
Foam-filled fenders, also known as solid fenders or polyurethane fenders, are cylindrical fenders made of a closed-cell foam core that is encapsulated with a tough polyurethane elastomer skin. The foam core provides buoyancy and energy absorption capabilities, while the polyurethane skin offers durability and resistance to abrasion, UV exposure, and chemicals.
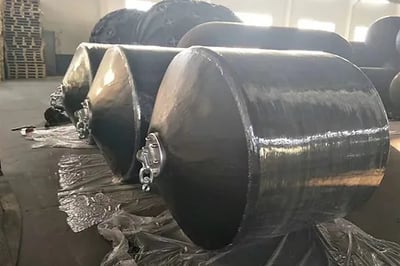
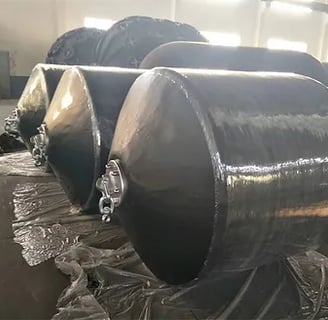
2) Applications
Foam-filled fenders are commonly used in various offshore and maritime applications, including ship-to-ship transfers, offshore platform protection, and as protective fenders for ports and harbors. They are effective in absorbing energy and reducing vessel impact forces during berthing and mooring operations. Foam-filled fenders are also suitable for use in harsh marine environments and in areas with limited maintenance capabilities.
3) Advantages and Disadvantages
Excellent energy absorption properties, making them suitable for both low-energy and high-energy berthing situations.
Low maintenance requirements due to their robust construction and resistance to punctures.
Can withstand harsh environmental conditions, including extreme temperatures and exposure to seawater, oil, and chemicals.
Can be customized in various sizes and shapes to suit specific requirements.
Disadvantages
Higher initial cost compared to pneumatic fenders.
Limited ability to withstand large berthing angles or excessive vessel sizes.
Bulkier and heavier than pneumatic fenders, making them more challenging to handle and store.
Benefits of Marine Rubber Fenders
1. Reduced Damage to Vessels and Structures
One of the primary benefits of marine rubber fenders is that they help to reduce damage to vessels and structures during berthing and mooring operations. By absorbing the impact energy of a vessel as it comes into contact with a quay wall or other structure, rubber fenders help to prevent damage to both the vessel and the structure.
1) Types of Damage that can be Prevented.
Some of the types of damage that can be prevented by using marine rubber fenders include
Hull damage to vessels, which can be caused by impact with a quay wall or other hard surface
Damage to berthing structures, such as piles, dolphins, or mooring bollards, which can be caused by the force of a vessel coming into contact with them
Damage to offshore structures, such as oil and gas platforms, which can be caused by the impact of vessels or by waves and currents
Damage to navigational aids, such as buoys and beacons, which can be caused by the force of waves and currents
2)Cost Savings from Reduced Damage
The use of marine rubber fenders can result in significant cost savings for port and harbor operators, vessel owners, and other stakeholders. By reducing the risk of damage to vessels and structures, rubber fenders can help to minimize repair and maintenance costs, as well as insurance premiums and liability claims.
For example, the cost of repairing hull damage to a vessel can range from thousands to millions of dollars, depending on the extent of the damage and the size of the vessel. Similarly, the cost of repairing damage to a quay wall or other berthing structure can be substantial, especially if the damage is severe or requires extensive repairs.
By using marine rubber fenders to reduce the risk of such damage, port and harbor operators can help to minimize these costs and ensure the long-term viability of their facilities.
2. Increased Safety for Personnel
Marine rubber fenders not only protect vessels and structures but also ensure the safety of personnel involved in berthing and mooring operations. These operations are inherently risky, and accidents can result in injuries, fatalities, and damage to equipment.
Using marine rubber fenders can reduce the risk of accidents by providing a cushioning effect that absorbs the impact of the vessel. This reduces the likelihood of personnel being caught in between the vessel and the dock or other structures, which is a common cause of accidents.
Additionally, marine rubber fenders can prevent vessels from surging forward or backward during berthing or mooring, which can also cause accidents. The fenders help to maintain the stability of the vessel, reducing the risk of capsizing or other accidents.
By reducing the risk of accidents, the use of marine rubber fenders can also lead to cost savings for companies. Accidents can result in insurance claims, legal fees, and downtime for repairs. By investing in marine rubber fenders, companies can reduce the likelihood of these costly incidents occurring.
3. Cost-Effective Solution
Compared to other types of protection systems, marine rubber fenders are a cost-effective solution for vessel and structure protection. While there are other systems available, such as concrete or steel barriers, these tend to be more expensive and less flexible.
Marine rubber fenders are a more flexible solution that can be customized to fit specific applications. This flexibility can result in cost savings by reducing the need for expensive modifications to existing structures or vessels.
Additionally, the reduced risk of accidents and damage to vessels and structures can result in significant cost savings over the long term. By investing in marine rubber fenders, companies can protect their assets and reduce the need for costly repairs or replacements.
4. Long Service Life
One of the key benefits of marine rubber fenders is their long service life. While the service life can vary depending on the type of fender and the conditions in which it is used, most marine rubber fenders have a service life of at least 10 years.
Several factors can affect the service life of marine rubber fenders, including exposure to UV light, abrasion, and environmental conditions such as temperature and humidity. However, by following proper maintenance and inspection procedures, the service life of marine rubber fenders can be extended.
Maintenance and Inspection Requirements
Proper maintenance and inspection are critical for ensuring the long service life of marine rubber fenders. Regular inspections should be conducted to check for signs of wear and tear, such as cracks, tears, or deformities.
Additionally, marine rubber fenders should be cleaned regularly to remove any dirt or debris that may accumulate on the surface. This can help to prevent the buildup of marine growth, which can damage the fender over time.
Conclusion
Marine rubber fenders are an essential component of vessel and structure protection in ports and harbors around the world. They provide a flexible and cost-effective solution for absorbing the impact of berthing and mooring operations, reducing the risk of damage to vessels and structures, and ensuring the safety of personnel.
With a range of types and sizes available, marine rubber fenders can be customized to fit specific applications, making them a versatile solution for a wide range of situations. By investing in marine rubber fenders, companies can protect their assets, reduce the risk of accidents, and realize long-term cost savings.
As a specialist provider of marine rubber fenders, Jettyguard offers a range of products and customization options to meet the unique needs of each customer. With a focus on quality and customer service, Jettyguard is committed to providing the best solutions for vessel and structure protection. Contact us today to learn more about how we can help with your marine rubber fender needs.